Tooling for Making Cues
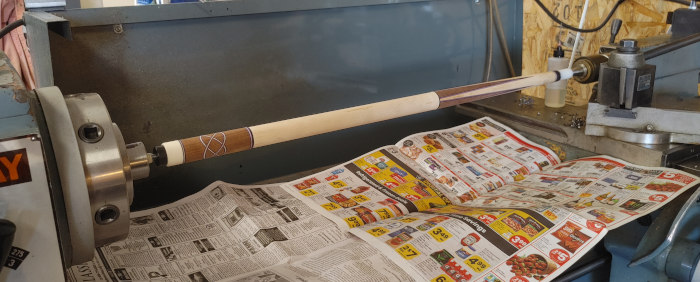
Making cues requires some specialty equipment, or modifications to standard equipment. There is a need to cut long, up to about 30", round wooden parts. These could be cut on a metal lathe with standard tooling, however the side load on the part will cause flex and loss of tolerance. Most cue makers use a router mounted to the cross slide of a lathe, live tooling. The router is moved along the bed, Z axis, as the part is rotated. An additional complication is cutting long tapers. On a lathe this can be done by offsetting the tailstock, using a taper attachment, or using a CNC lathe.
Many of the elements above are already in a CNC router. If a rotary axis, which can take a 30" part, is added this direction would work very well. The swing of the lathe/axis only needs to accommodate the stock for a cue, maybe 2" diameter.
In addition to cutting long tapers, the cue maker needs to do accurate joint machining. This is best done on a metal lathe, much easier than trying to modify a wood lathe. One requirement is that the cue pass through the head stock of the lathe.
Cue lathes are available. I don't have a good definition of a cue lathe, there are many types and variations. One common feature is a second 3-jaw chuck at the back end of the tailstock. Then a cue can be held centered at two point.
Note that I have little or no experience building cues. The above is my take from my research, mostly YouTube.
My Direction
I looked at the equipment I have and thought I could build a cue or two. I decided to use my CNC converted knee mill. It has a 9"x42" table which should fit the length of a cue butt. Most of the cutting can be done in two parts, forearm and handle, making this even more feasible. I also have a Sherline combination machine which includes a lathe. I decided to mount the Sherline lathe on the knee mill table. The head and the tailstock needs to be separated to get 30" but this is possible. In fact, Sherline sells sections of lathe bed for use as a cue lathe. After some figuring I made two head mounting blocks. They mount on the mill table and hold the headstock of the Sherline. I ordered a tailstock bed section from Sherline for the other end.
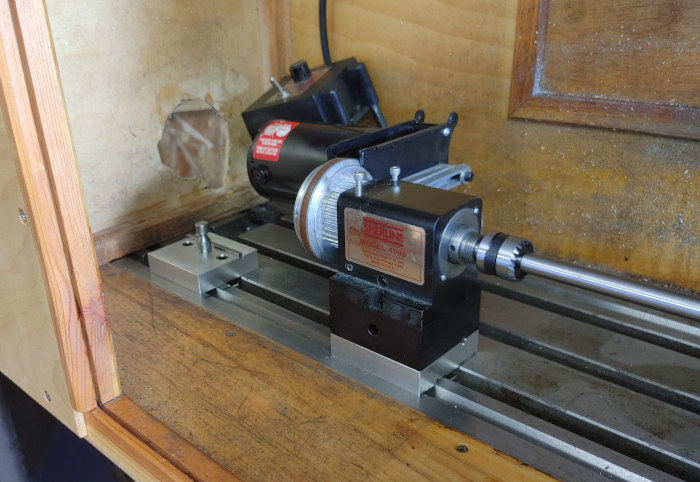
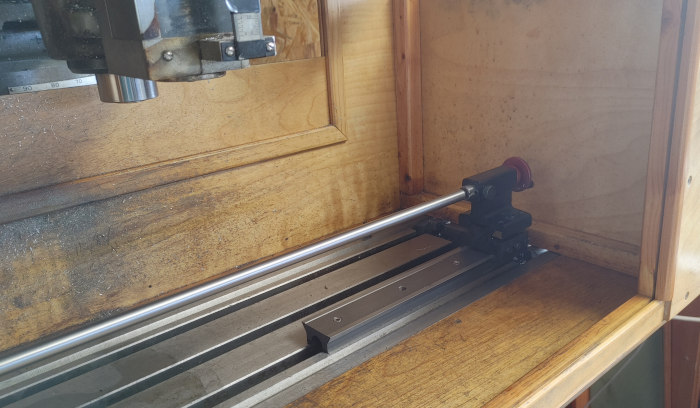
It takes some time and effort to align the headstock with the tailstock. This needs to be within a few thousands, but the more aligned the better. The metal rod in the pictures is used for alignment. Wood blanks are mounted on centers as the metal rod is in these pics. A driving center is in the headstock which works fairly well. It slips a little but since this setup is for round parts that's OK.
I have a Porter Cable trim router that I mounted on the spindle. For woodworking the higher speed spindle is needed (or we'd be standing there all day).
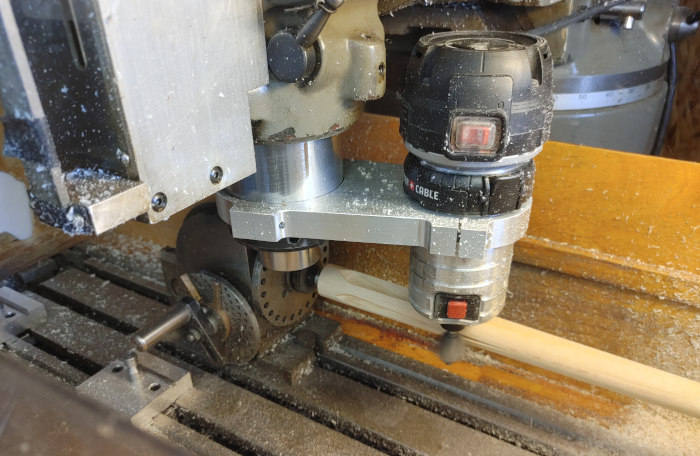
I need to accurately hold and rotate the forearm to cut V slots for points. Well, I have a dividing head that is made to do that. The picture just above and the one below show this dividing head mounted. For points I first used a driving center which did not work. The part moved enough on this center that the V grooves were not straight. I put a three jaw chuck on the dividing head which held the part much more solidly. These pictures also show how point grooves are cut.
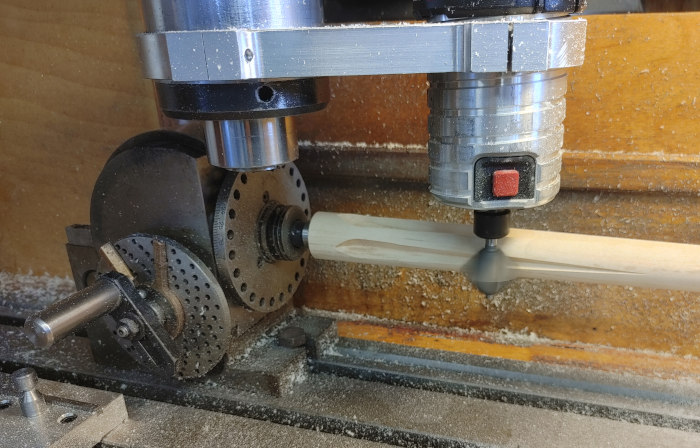
The box seen on the knee mill is to catch chips. It works well and should help control wood chips as well as metal.
I have a 14" lathe with, I think, 1 3/8" through hole. It only has a 33" bed (a 14x33 lathe). That length is tight for the full butt but workable. The joint work is done on this lathe using standard machining practices. Holding a tapered part in the lathe is needed though. I make nylon tapered sleeves or collets as needed to hold the cue in three and four jaw chucks. The chuck jaws are some 2" deep which gives a good hold.
It isn't good practice to cut wood on machine tools. Sawdust/oil mix is abrasive and can cause trouble if it gets into the ways, similar to grinding dust. So precautions are taken by covering open ways and cleaning tools after use. This isn't too bad on my mill as the chip box catches most of the sawdust and the ways are away from the table. The lathe ways are open so more care is called for there.
This is not optimum tooling for cues. Turns out the travel of the knee mill is noticeably shorter than the 42" table length. An assembled cue butt can be held in the Sherline lathe on the knee mill, but it's full length can't be cut in one go. Thus, half its length is cut on centers, then flipped end for end and the other half machined. This works well for cutting on centers with the accuracy of the CNC mill, but more trouble than with more appropriate machines. Additionally, careful set-up is needed to avoid interference between the knee mill spindle and other equipment, like the dividing head. This problem is evident in the pictures above. Notice the speed control box for the Sherline has been moved for clearance.
Another potential problem is the wood router. It works fine with larger cutters but I strongly suspect the run-out is too large for the small cutters used for inlays. Inlays require cutters on the order of 0.020" diameter. I understand the run-out of the typical router is some 0.005". Run-out a large percentage of the cutter diameter is likely to cause problems, i.e. broken endmills. A true spindle would be a much better choice, but the trim router was available. I've wanted a high speed auxiliary spindle for many years for use with small endmills. This project may push the needle enough to buy one.
A CNC fourth axis is needed for engraving. I've wanted a fourth axis since I converted the knee mill some 20 years ago. I'm currently thinking of getting a second Sherline head stock and installing a stepper motor on it. This would fit right on the blocks I've made and share tooling with the already mounted Sherline lathe. It would be an fairly simple project. Not optimum as a general purpose fourth axis, but would work fine for cues and other small parts.
So at least initially, for a few cues, I'll use the motto "use what ya got".
Cues : Main Page Cue #1